Real-Time Process Optimization For Open Pit Iron Ore Mines
Real-Time Process Optimization for Open Pit Iron Ore Mines
Introduction
Open pit iron ore mining operations are complex and involve multiple stages, from drilling and blasting to hauling, crushing, milling, and final transport. Ensuring efficiency, productivity, and sustainability across these stages is crucial for maintaining competitive advantage and operational excellence.
XMPro’s Intelligent Business Operations Suite (iBOS) offers a powerful real-time process optimization solution that integrates data from various stages of the mining process into a single, comprehensive dashboard. This solution provides unparalleled visibility into key performance metrics, enabling proactive management and optimization of mining operations. By leveraging advanced analytics and predictive capabilities, XMPro iBOS delivers actionable insights and recommendations that help operators streamline operations, reduce costs, and enhance overall performance.
This unified approach ensures that all aspects of the mining process are monitored and optimized in real time, from maintaining high product quality to achieving compliance with environmental and safety standards. With XMPro iBOS, mining operators can achieve optimal efficiency, address issues before they escalate, and drive sustainable operational improvements.
The Challenge
Open pit iron ore mining operations face numerous challenges that can impact efficiency, productivity, and sustainability. These challenges are:
Complexity of Multi-Stage Operations: Managing the intricate processes from drilling and blasting to hauling, crushing, milling, and final transport requires seamless coordination and real-time visibility into each stage. Any inefficiency or bottleneck in one stage can cascade and disrupt the entire operation.
Throughput Variability: Inconsistent production rates across different stages of the mining process can lead to fluctuations in overall output. Variability in throughput can be caused by equipment performance, material characteristics, and operational inefficiencies.
Equipment Reliability and Maintenance: Mining equipment is subjected to harsh conditions, leading to wear and tear. Ensuring the reliability of critical assets and minimizing unplanned maintenance is essential to avoid operational disruptions and high maintenance costs.
Energy Consumption and Environmental Impact: High energy consumption and CO2 emissions are significant concerns in mining operations. Inefficient processes not only increase operational costs but also contribute to a larger environmental footprint, challenging sustainability goals.
Product Quality Management: Maintaining consistent product quality, especially the iron content (Fe) of the ore, is critical. Variations in product quality can affect downstream processing and customer satisfaction.
Tailings Management: Efficiently managing the generation and storage of tailings is crucial for environmental compliance and operational efficiency. Excessive tailings generation can lead to storage capacity issues and regulatory non-compliance.
Safety and Compliance: Ensuring worker safety and adhering to environmental, social, and governance (ESG) standards are paramount. High injury rates and non-compliance with safety regulations can lead to legal repercussions and damage to the company’s reputation.
Data Integration and Real-Time Visibility: Integrating data from multiple sources and providing real-time visibility into operations is a significant challenge. Incomplete or inaccurate data can hinder effective decision-making and process optimization.
Actionable Insights and Predictive Capabilities: Generating actionable insights from vast amounts of data and predicting potential issues before they escalate is essential for proactive management. Without advanced analytics and predictive tools, mining operations may struggle to address problems promptly and efficiently.
By addressing these challenges, XMPro iBOS provides a comprehensive solution that enhances visibility, improves operational efficiency, and supports sustainable mining practices.
The Solution: XMPro iBOS for Real-Time Process Optimization in Open Pit Iron Ore Mines
XMPro’s Intelligent Business Operations Suite (iBOS) offers a comprehensive real-time process optimization solution that addresses the multifaceted challenges of open pit iron ore mining. By integrating data from various stages of the mining process into a single, cohesive dashboard, XMPro iBOS provides unparalleled visibility and actionable insights to enhance efficiency, reduce costs, and ensure sustainability.
Data Integration & Real-Time Monitoring
XMPro iBOS leverages the Data Stream Designer and our extensive agent library to integrate data from drilling, blasting, loading, hauling, crushing, milling, screening, stockpiling, and transportation stages into a unified solution. This includes operational, tactical, and strategic views in real-time. This real-time monitoring capability allows operators to maintain continuous oversight of all processes, promptly identify bottlenecks, and take corrective actions to ensure smooth operations.
Predictive Analytics & Maintenance
Utilizing advanced machine learning algorithms, XMPro iBOS analyzes operational data to predict equipment failures and maintenance needs. Predictive maintenance alerts help prevent unplanned downtime by scheduling maintenance activities at optimal times, thereby extending the lifespan of critical assets and reducing maintenance costs.
Performance Optimization
XMPro iBOS continuously monitors key metrics such as production throughput, fuel consumption, CO2 emissions, and iron ore grade. It provides real-time insights and recommendations to optimize energy use, maintain product quality, and manage tailings efficiently, ensuring compliance with environmental regulations and enhancing overall operational efficiency.
Configurable Dashboards
The system features configurable dashboards that display critical KPIs such as production output, product quality, asset reliability, energy consumption, CO2 emissions, and worker safety metrics. These dashboards offer clear visuals and detailed analysis, empowering operators to make data-driven decisions and optimize operations.
Real-Time Alerts and Notifications
XMPro iBOS features a robust Recommendation Manager that generates real-time recommendations and alerts based on predictive analytics and data analysis. The Recommendation Manager continuously monitors operational data to detect anomalies and deviations from expected performance. When issues such as excessive energy consumption or deviations in product quality are identified, the system immediately sends alerts to the relevant personnel. These real-time notifications ensure that problems are addressed promptly, minimizing the impact on operations.
Beyond alerts, the Recommendation Manager provides actionable recommendations to resolve identified issues. For example, if the system detects a spike in energy consumption, it might recommend specific operational adjustments or maintenance activities to optimize fuel use and reduce emissions. Similarly, for product quality deviations, the system could suggest adjustments to processing parameters to maintain iron ore grade specifications.
The Recommendation Manager plays a crucial role in closing the loop on event response. By providing clear, actionable steps alongside alerts, it ensures that operators not only recognize issues but also have a roadmap for resolving them. This proactive approach minimizes downtime and enhances operational efficiency.
AI Assistant for Proactive Insights
The XMPro AI Assistant enhances decision-making by answering specific queries and providing proactive insights based on historical and real-time data. This tool helps operators understand the root causes of issues, such as high idle times or throughput variability, and suggests effective solutions.
Discover XMPro’s Solution For Real-Time Process Optimization for Open Pit Iron Ore Mines
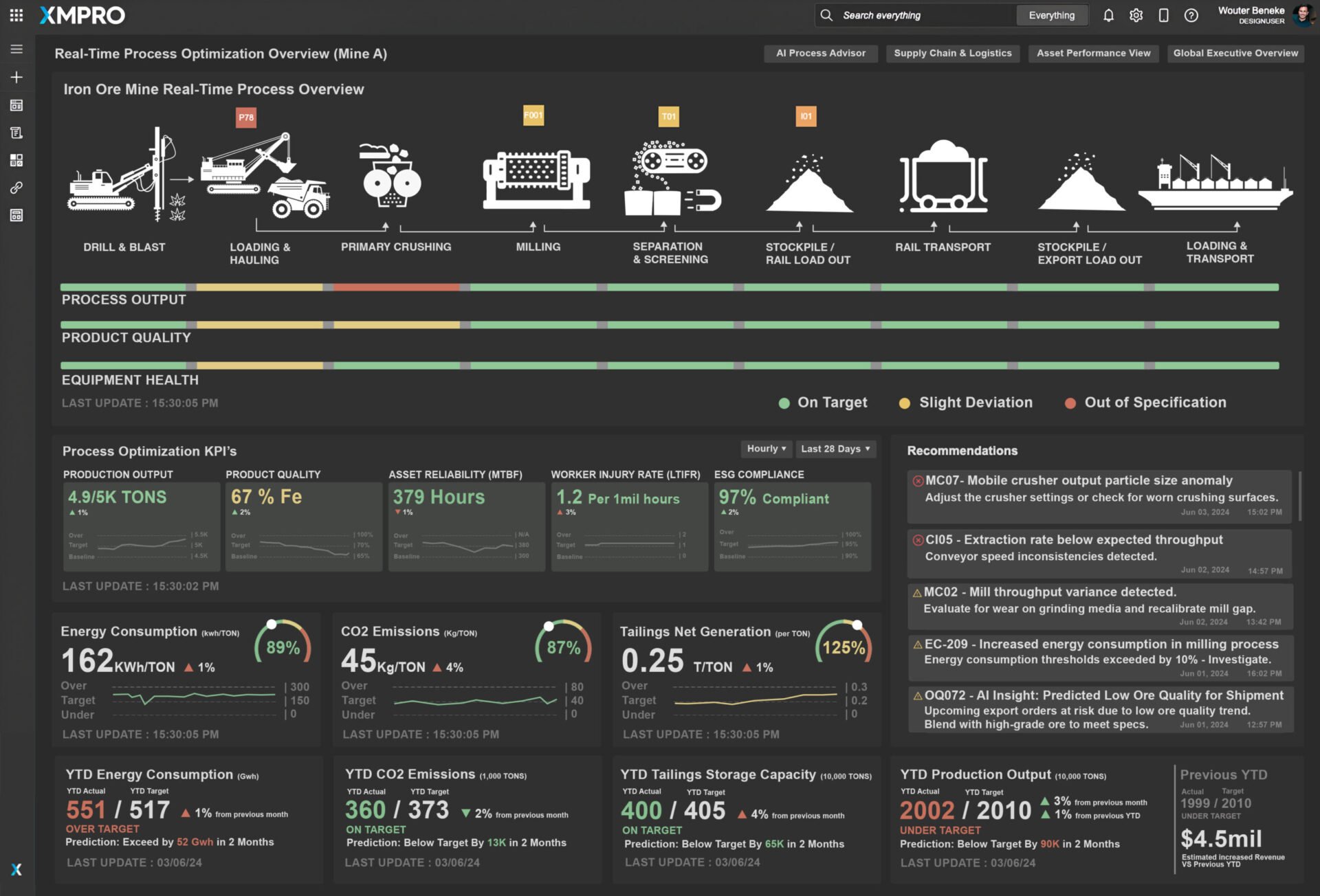
Figure 1: Real-Time Process Optimization Overview – Mine A
The Real-Time Process Optimization Overview provides a comprehensive view of the entire iron ore mining process at Mine A, from drilling and blasting to final loading and transport. This dashboard integrates data across various stages, offering operators critical insights into performance metrics, enabling effective management and optimization of mining activities.
Process Overview The dashboard displays a visual representation of the different stages in the mining process:
- Drill & Blast
- Loading & Hauling
- Primary Crushing
- Milling
- Separation & Screening
- Stockpile/Rail Load Out
- Rail Transport
- Stockpile/Export Load Out
- Loading & Transport
Status Indicators Color-coded status indicators show the performance of each process stage in terms of process output, product quality, and equipment health:
- Green: On Target
- Yellow: Slight Deviation
- Red: Out of Specification
Key Performance Indicators (KPIs) The dashboard highlights critical KPIs for process optimization:
- Production Output: Real-time tracking of total production output in tons, comparing actual vs. target to ensure consistent production rates.
- Product Quality: Measurement of the iron content (Fe) percentage in the ore to maintain consistent product quality.
- Asset Reliability (MTBF): Mean time between failures for equipment, reflecting reliability and maintenance needs.
- Worker Injury Rate (LTIFR): Lost time injury frequency rate, providing insights into safety performance.
- ESG Compliance: Environmental, social, and governance compliance percentage, indicating adherence to regulatory and sustainability standards.
Energy and Environmental Metrics
- Energy Consumption (kWh/TON): Tracking of energy used per ton of ore processed, highlighting efficiency and cost.
- CO2 Emissions (Kg/TON): Measurement of CO2 emissions per ton of ore processed, important for environmental impact.
- Tailings Net Generation (t/TON): Amount of tailings generated per ton of ore, indicating waste management efficiency.
- Year-to-Date (YTD) Metrics: Summarized YTD energy consumption, CO2 emissions, and storage capacity for tailings.
Drill-Down Capabilities XMPro iBOS allows operators to drill down into each step of the process, providing detailed views oriented towards process efficiency, product quality, and asset reliability/equipment health:
- Process Efficiency: Detailed drill-down views for each stage (e.g., loading & hauling, crushing, milling) enable operators to analyze specific inefficiencies and optimize processes. This can include cycle time analysis, throughput metrics, and bottleneck identification.
- Product Quality: Operators can drill down into quality metrics at each stage to ensure the ore meets the required specifications. Real-time monitoring and adjustments can be made to maintain the desired iron content and overall product quality.
- Asset Reliability/Equipment Health: Detailed asset health views provide insights into the reliability and maintenance needs of critical equipment. This includes tracking mean time between failures (MTBF), monitoring equipment conditions, and scheduling predictive maintenance to prevent unplanned downtime.
Actionable Recommendations and Alerts The dashboard provides real-time recommendations and alerts based on data analysis and predictive analytics:
- MC07: Mobile crusher output particle size anomaly – Suggests adjusting the crusher settings or checking for worn crushing surfaces.
- CI05: Extraction rate below expected throughput – Indicates conveyor speed inconsistencies.
- MC02: Mill throughput variance detected – Recommends evaluating the wear on grinding media and recalibrating mill gaps.
- EC-209: Increased energy consumption in milling process – Prompts investigation of energy usage.
- QO072: AI Insight – Predicted low ore quality for shipment – Suggests blending with high-grade ore to meet specs.
Operational Insights and Key Benefits
- Increased Productivity: By identifying and addressing inefficiencies, the dashboard helps to boost overall productivity.
- Cost Savings: Optimizing energy consumption and reducing maintenance costs contribute to substantial cost savings.
- Enhanced Equipment Longevity: Proactive maintenance recommendations extend the lifespan of critical assets.
- Environmental Compliance: Improved fuel efficiency and reduced emissions ensure compliance with environmental regulations.
- Safety and Compliance: Enhanced visibility into operations helps maintain safety standards and regulatory compliance.
By leveraging the Real-Time Process Optimization Overview, mining operations can achieve enhanced visibility, improve productivity, and drive sustainable operational improvements, maintaining a competitive edge in the industry.
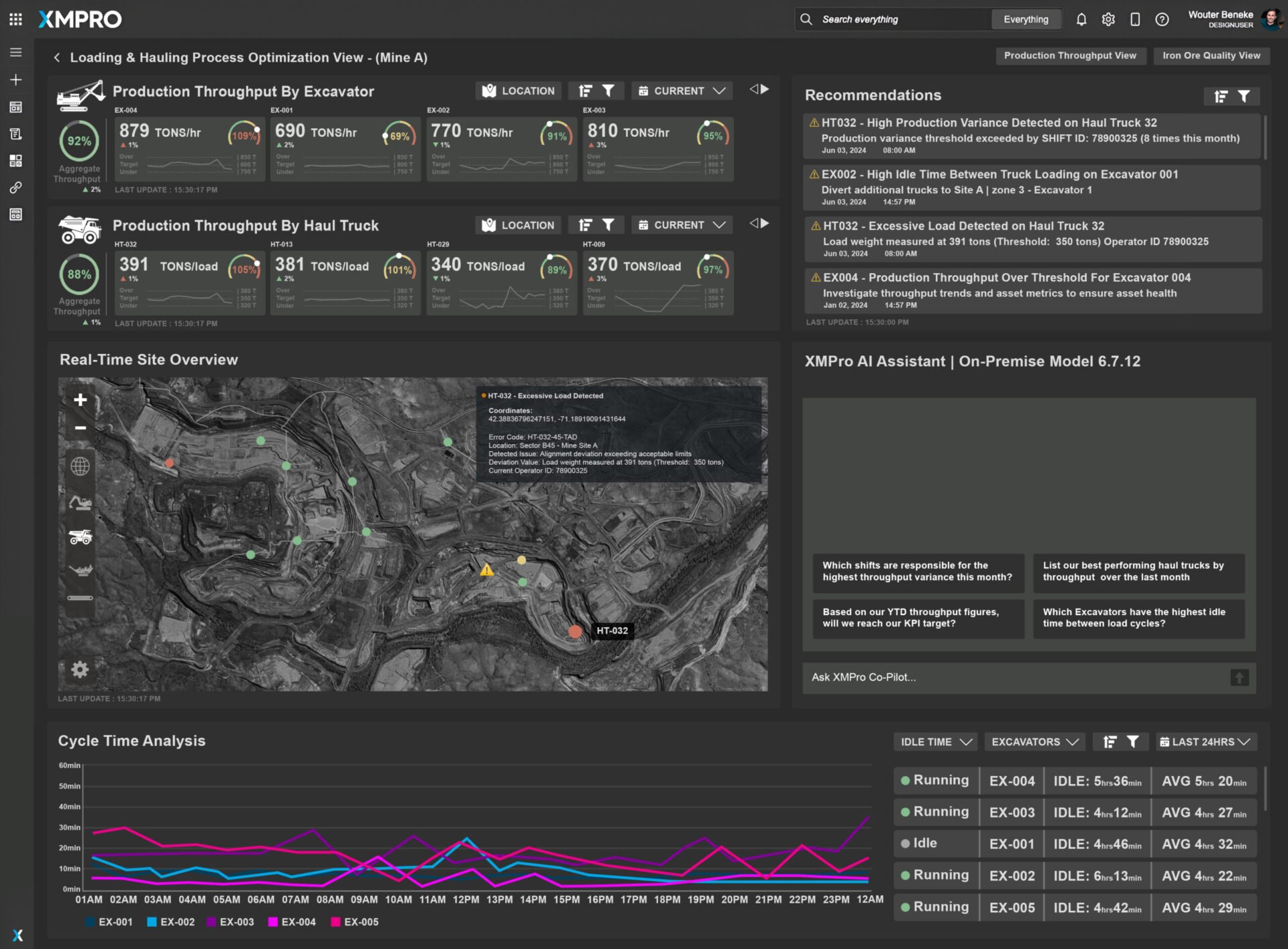
Figure 2: Drilldown View of Loading & Hauling Process Optimization – Mine A
The Loading & Hauling Process Optimization View is instrumental for monitoring and optimizing the operational efficiency of loading and hauling activities in iron ore mining operations. This dashboard provides critical insights into various performance metrics, enabling effective management and optimization of these activities to enhance productivity and reduce operational costs.
Production Throughput by Excavator The dashboard displays throughput metrics for each excavator, including actual versus target throughput in tons per hour. This helps manage productivity by identifying deviations from targets and ensuring optimal asset utilization. For example, consistently falling short of targets may indicate the need for maintenance or operational adjustments.
Production Throughput by Haul Truck Throughput metrics for haul trucks are also shown, detailing actual tons per load compared to target values. This data assists in managing load efficiency and identifying discrepancies. High variance in load weights might suggest issues with loading accuracy or truck capacity utilization.
Real-Time Site Overview The real-time site overview provides a visual representation of the mining site, including the locations of all assets and their current status. This helps in monitoring the overall operation and improving coordination. Identifying areas with high idle times can lead to better planning and resource allocation.
Cycle Time Analysis Analyzes the cycle times for both excavators and haul trucks, presenting data on how long each phase of the cycle takes. This analysis helps pinpoint inefficiencies and bottlenecks in the loading and hauling process. Longer-than-average cycle times may indicate delays in loading or unloading, poor route planning, or equipment issues.
Idle Time Analysis Idle time analysis provides a breakdown of idle times for different assets, highlighting the average idle time over the last 24 hours. This helps identify causes of idle times and enables actions to reduce these periods, improving overall asset utilization. High idle times could be due to poor scheduling, coordination issues between loading and hauling, or equipment downtime.
Recommendations and Alerts The dashboard includes actionable recommendations and real-time alerts based on data analysis. These provide insights into potential issues and suggest corrective actions. For example, alerts for high idle times or excessive load weights prompt immediate operational adjustments to mitigate these issues.
XMPro AI Assistant Queries XMPro AI Assistant generates further insights by querying real-time and historical data. These queries can address questions such as which shifts are responsible for the highest throughput variance or which excavators have the highest idle times between load cycles. This aids in proactive decision-making and continuous improvement.
Key Benefits
Increased Productivity By identifying and reducing idle times, optimizing cycle times, and ensuring efficient load distribution, overall productivity is significantly enhanced.
Cost Savings Lower operational costs are achieved through reduced idle times, optimized fuel consumption, and improved cycle efficiency. This leads to significant cost savings.
Enhanced Equipment Longevity Proactive maintenance and operational insights extend the lifespan of both excavators and haul trucks, reducing the need for frequent replacements.
Environmental Compliance Improved fuel efficiency and reduced emissions contribute to better compliance with environmental regulations and sustainability goals.
Safety and Compliance Enhanced visibility into operations and proactive maintenance help maintain safety standards and regulatory compliance.
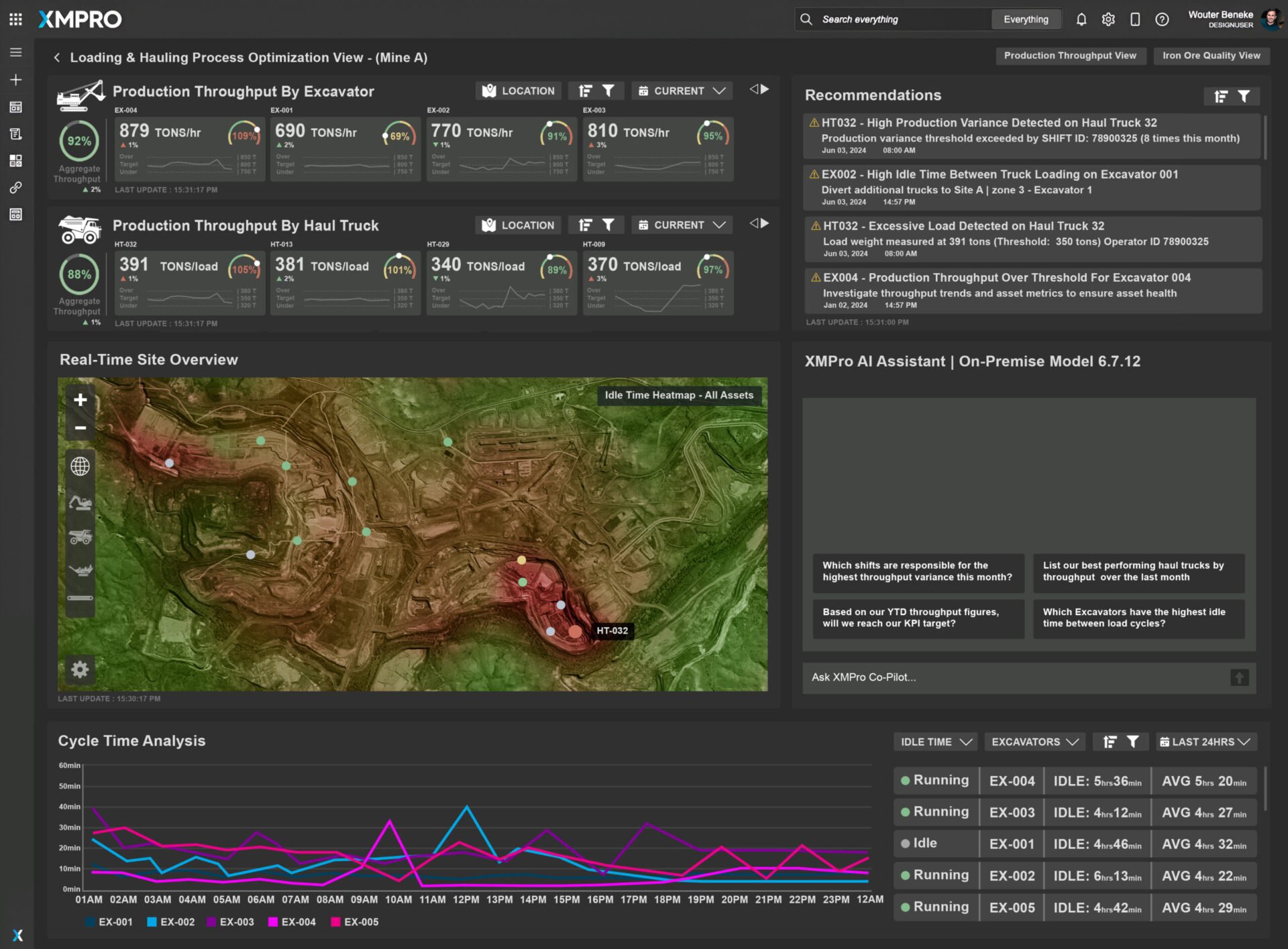
Figure 3: Idle Time Heatmap – Loading & Hauling Process Optimization View – Mine A
Real-Time Site Overview with Idle Time Heatmap The real-time site overview with the idle time heatmap provides a visual representation of the mining site, including the locations of all assets and their current status, with a specific focus on idle times. The heatmap highlights areas with high idle times, allowing for easy identification of inefficiencies. This visualization helps in monitoring overall operations and improving coordination. For instance, areas with concentrated idle times can be targeted for process improvements or resource reallocation.
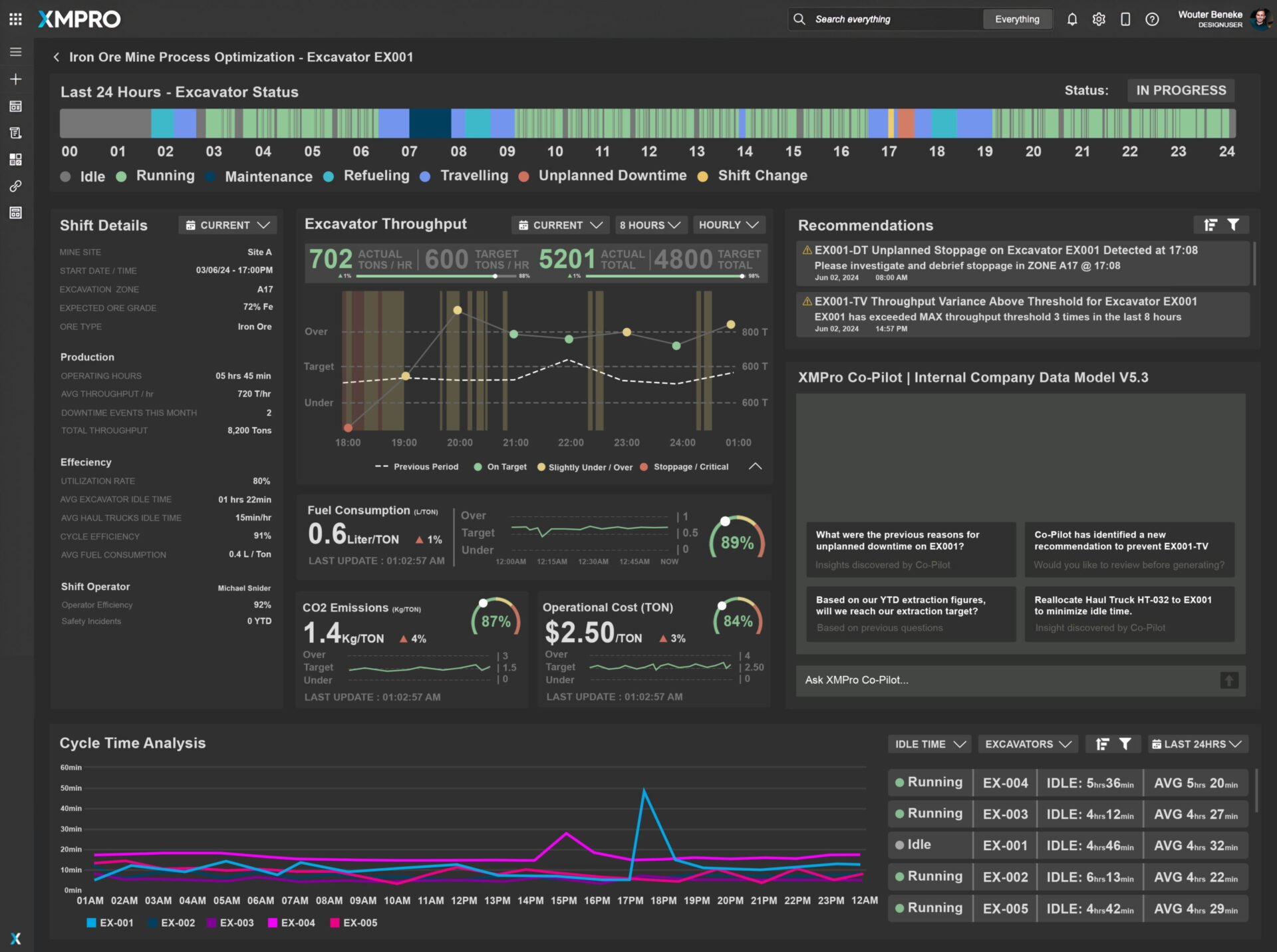
Figure 4: Drilldown Asset Analysis View – Mobile Asset Process Optimization
The Drilldown Asset Analysis View is crucial for monitoring and optimizing the operational efficiency of mobile assets such as excavators, haul trucks, and mobile crushers in iron ore mining operations. This dashboard provides detailed insights into various performance metrics, enabling effective management and optimization of these assets to enhance productivity and reduce operational costs.
Mobile Asset Status Timeline The visual representation of the status of mobile assets over the last 24 hours, including running, idle, maintenance, refueling, traveling, unplanned downtime, and shift changes, identifies patterns of inefficiency and informs better scheduling and resource allocation. For example, frequent idle periods may highlight issues with coordination or poor shift planning.
Shift Details Detailed shift information, such as mine site, excavation zone, expected ore grade, and production metrics like operating hours and average throughput, offers a snapshot of current operations, aiding in real-time decision-making and performance tracking. Insights can include recognizing shifts with higher productivity or identifying zones with more frequent downtime.
Mobile Asset Throughput Throughput metrics display actual versus target throughput in tons per hour for mobile assets, helping to manage productivity, identify deviations, and ensure optimal asset utilization. This can reveal whether the equipment is consistently underperforming or exceeding targets, prompting adjustments to operational strategies.
Fuel Consumption Monitoring fuel consumption and CO2 emissions for mobile assets provides insights into fuel efficiency and environmental impact, essential for reducing operational costs and achieving sustainability goals. For instance, unexpected increases in fuel consumption might indicate engine inefficiencies or the need for maintenance.
Operational Cost The operational cost per ton metric offers a clear view of financial efficiency, highlighting cost-saving opportunities. Insights might include identifying high-cost periods and correlating them with specific operational activities or maintenance events.
Cycle Time Analysis Cycle time and idle time analyses pinpoint inefficiencies in the excavation, loading, and hauling processes, addressing issues related to planning and improving overall efficiency. For example, longer cycle times may suggest bottlenecks in the process or delays in asset availability.
Idle Time Analysis Idle time analysis highlights the average idle time over the last 24 hours for different mobile assets, identifying causes of idle times and enabling actions to reduce idle periods and improve asset utilization. This can reveal if specific assets are idling more frequently, suggesting targeted improvements.
Recommendations and Alerts The dashboard provides actionable recommendations and real-time alerts based on data analysis, offering insights into potential issues and suggesting corrective actions. For example, an alert for high fuel consumption could lead to immediate checks and preventive measures.
XMPro AI Assistant Queries XMPro AI Assistant queries generate further insights, aiding proactive decision-making and continuous improvement. These queries might include analysis of reasons for unplanned downtime or suggestions for improving operator performance based on historical data.
Key Benefits
Increased Productivity By identifying and reducing idle times, optimizing throughput, and addressing inefficiencies, productivity is significantly enhanced. For example, aligning shift changes with optimal operational periods can boost overall productivity.
Cost Savings Lower fuel consumption, reduced maintenance costs, and improved operational efficiency lead to substantial cost savings. Identifying and mitigating periods of high operational cost can significantly reduce expenses.
Enhanced Equipment Longevity Proactive maintenance and operational insights extend the lifespan of mobile assets, reducing the need for frequent replacements. This ensures that equipment is maintained before issues become critical.
Environmental Compliance Improved fuel efficiency and reduced emissions contribute to better compliance with environmental regulations and sustainability goals. Monitoring CO2 emissions helps maintain adherence to regulatory standards.
Safety and Compliance Enhanced visibility into operations and proactive maintenance help maintain safety standards and regulatory compliance. Ensuring that mobile asset operations are within safe parameters reduces the risk of accidents.
By leveraging the Drilldown Asset Analysis View for mobile assets, mining operations can achieve enhanced visibility into their processes, leading to improved productivity, cost savings, and optimized resource utilization.
Why XMPro iBOS for Mining Plant Operations?
XMPro’s Intelligent Business Operations Suite (iBOS) is expertly designed to tackle the complex challenges in process optimization and asset performance management in open pit iron ore mining. Here’s the transformation it brings:
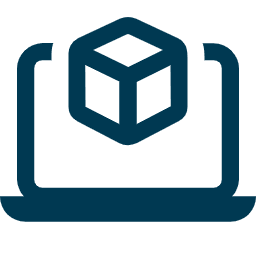
Advanced Intelligent Digital Twin Modeling:
XMPro iBOS constructs sophisticated digital twins, reflecting the detailed operations of mining equipment. It allows comprehensive performance analysis under varied conditions, vital for operational optimization.
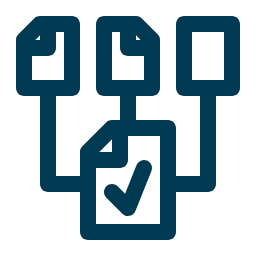
Advanced Sensor Data Integration & Transformation:
Real-time sensor data across mobile assets offer critical insights into performance metrics like vibration, load capacity, and engine status, which are essential for detecting early signs of potential failures and maintenance needs.
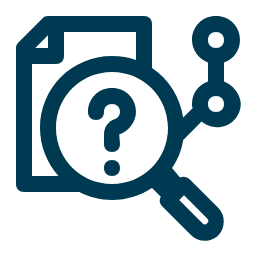
Predictive Analytics for Performance Enhancement:
Utilizing advanced analytics, XMPro iBOS predicts potential asset failures, enhancing operational parameters and enabling preventive adjustments, thereby ensuring continuous mining operations with minimized downtimes.
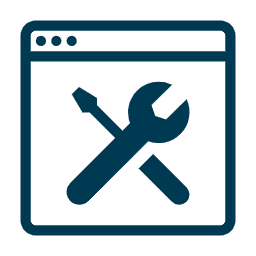
Maintenance Scheduling Optimization:
Performance data drives XMPro iBOS’s maintenance scheduling, transforming the approach from reactive to proactive, optimizing the maintenance cycle for various assets, and significantly reducing breakdowns.
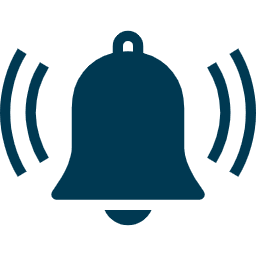
Real-Time Monitoring and Predictive Alerting:
Real-time monitoring and predictive alerting are critical components of XMPro’s iBOS for managing mobile assets within the mining industry. This ensures each mobile asset, from haul trucks to dozers, functions within the optimal parameters, thus enhancing efficiency and reducing reliance on manual intervention.
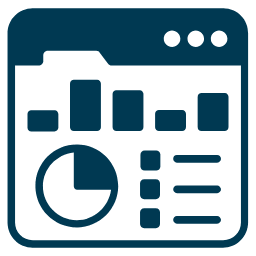
Configurable and Interactive Dashboards:
XMPro provides configurable dashboards that offer real-time insights into the health and performance of equipment across all dairy processing plants. These dashboards are designed to be interactive, enabling detailed scrutiny of specific operational aspects and supporting centralized management decisions.
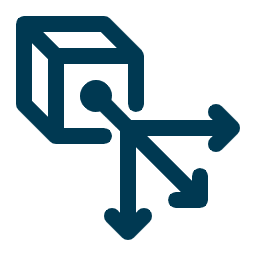
Scalability and Flexibility – Start Small, Scale Fast:
Designed to accommodate dairy operations of any scale, XMPro’s modular architecture allows for seamless integration and adaptability. This scalability ensures that mining plants can efficiently manage operations as they expand or adapt to changing market demands.
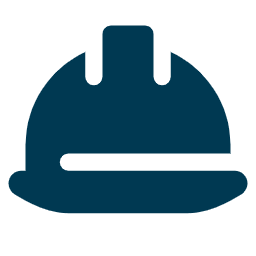
Enhanced Safety & Operational Efficiency:
XMPro boosts operational safety by identifying potential hazards and inefficiencies in the processing line, ensuring that all equipment operates within safe and optimal parameters. This contributes to a safer working environment and more efficient production processes.
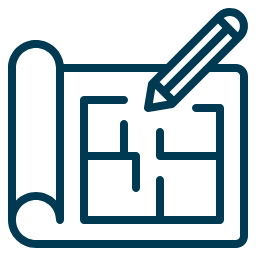
XMPro Blueprints – Quick Time to Value:
Offering quick time-to-value, XMPro Blueprints facilitate rapid deployment of intelligent operations solutions across mining operations. These templates are built on industry best practices, ensuring that plants can quickly realize the benefits of digital transformation.
XMPro iBOS caters to the predictive maintenance needs of the mining industry’s mobile assets with a suite that promises comprehensive, predictive, and integrated solutions, driving efficiency and safety across operations.
