Golden Batch For Culture Addition In The Dairy processing Industry.
Golden Batch for Culture Addition in the Dairy Processing Industry
Introduction
In the dairy processing industry, the addition of cultures (beneficial bacteria) is a critical step in the production of yogurt, cheese, and other fermented dairy products. Achieving the “Golden Batch” in culture addition means consistently reaching the optimal mix of cultures, temperature, and incubation times to produce dairy products of superior quality, taste, and texture. This use case explores how XMPro’s Intelligent Digital Twin Suite (iDTS) can optimize the culture addition process, ensuring each batch meets these high standards.
The Challenge
Achieving the Golden Batch in culture addition within the dairy processing industry entails mastering a series of intricate challenges: ensuring the viability and precise measurement of cultures, maintaining optimal fermentation conditions, and consistently producing high-quality fermented dairy products. These challenges are compounded by the need to adhere to stringent safety and quality standards while optimizing production efficiency and minimizing waste. Addressing these issues effectively is crucial for dairy processors aiming to maintain product excellence, operational efficiency, and compliance with regulatory standards, highlighting the importance of adopting advanced solutions like the Golden Batch for Culture Addition.
Consistency in Culture Viability: Ensuring the added cultures are alive and active to initiate proper fermentation.
Optimal Fermentation Conditions: Maintaining precise temperature and pH levels throughout the fermentation process.
Product Quality and Safety: Achieving consistent product quality while adhering to safety and regulatory standards.
Efficiency in Production: Maximizing yield and minimizing waste during the culture addition and fermentation processes.
The Solution: XMPro’s Intelligent Golden Batch Solution for Culture Addition in the Dairy Industry.
XMPro’s Intelligent Digital Twin Suite (iDTS) is expertly crafted to tackle the specific challenges of culture addition in the dairy processing industry. By delivering a targeted and integrated solution, it revolutionizes the process of managing culture viability, precision in addition, and fermentation conditions, ensuring the highest standards of product consistency and quality. Leveraging the advanced functionalities of XMPro iDTS, this strategy transforms culture addition into a controlled, replicable process, ensuring each batch meets the golden standard for fermented dairy products, while also upholding efficiency, quality assurance, and compliance with safety standards.
Key Features
Advanced Sensor Data Integration & Transformation:
XMPro’s iDTS platform is engineered to integrate sensor-derived data in real-time, capturing essential parameters such as temperature, quality measures, and flow rates at the initial milk collection phase. This integration is crucial for the prompt detection of raw milk quality variances and potential process bottlenecks. The system ensures continuous monitoring at milk reception, quickly identifying any discrepancies that could affect quality or cause logistical inefficiencies.
Real-time Batch Monitoring and AI Quality Prediction:
This solution offers comprehensive oversight of milk batches by capturing details like batch identity, volume, and supplier specifics. It continuously compares real-time metrics such as temperature, fat and protein contents, pH levels, and somatic cell counts to ideal standards. Leveraging AI, the platform forecasts milk quality, offering actionable insights such as blending options to achieve desired fat content, thereby ensuring quality benchmarks are met.
Visualization of Process Timelines and Storage Capacities:
The platform enables users to visually track each phase in the dairy processing sequence, from the initial milk collection to the final aging stage, with up-to-the-minute updates on storage capacity levels. This functionality ensures efficient progression through the various stages of production.
Operational Performance and Energy Utilization Insights:
XMPro delivers valuable insights into the plant’s operational performance, featuring key metrics such as energy efficiency, Overall Equipment Effectiveness (OEE), and Total Effective Equipment Performance (TEEP). These insights support strategic decision-making to enhance energy consumption efficiency and boost production yields.
Predictive Recommendations:
The XMPro system anticipates and issues suggestions to preemptively address process-related issues, including concerns about culture activity, texture adjustments, and the optimization of parameters for processes like pasteurization. Guidance is also provided for critical pre-commencement checks and throughout the aging process.
Interactive and Customizable Dashboards:
Equipped with an interactive dashboard interface, XMPro provides operators with real-time batch status, a retrospective line status over the past day, and analysis of the current month’s downtime causes. Process enhancement recommendations are also delivered through this interface, promoting informed decision-making and operational efficiency.
Discover XMPro’s Golden Batch Solution for Culture Addition in the Dairy Processing Industry
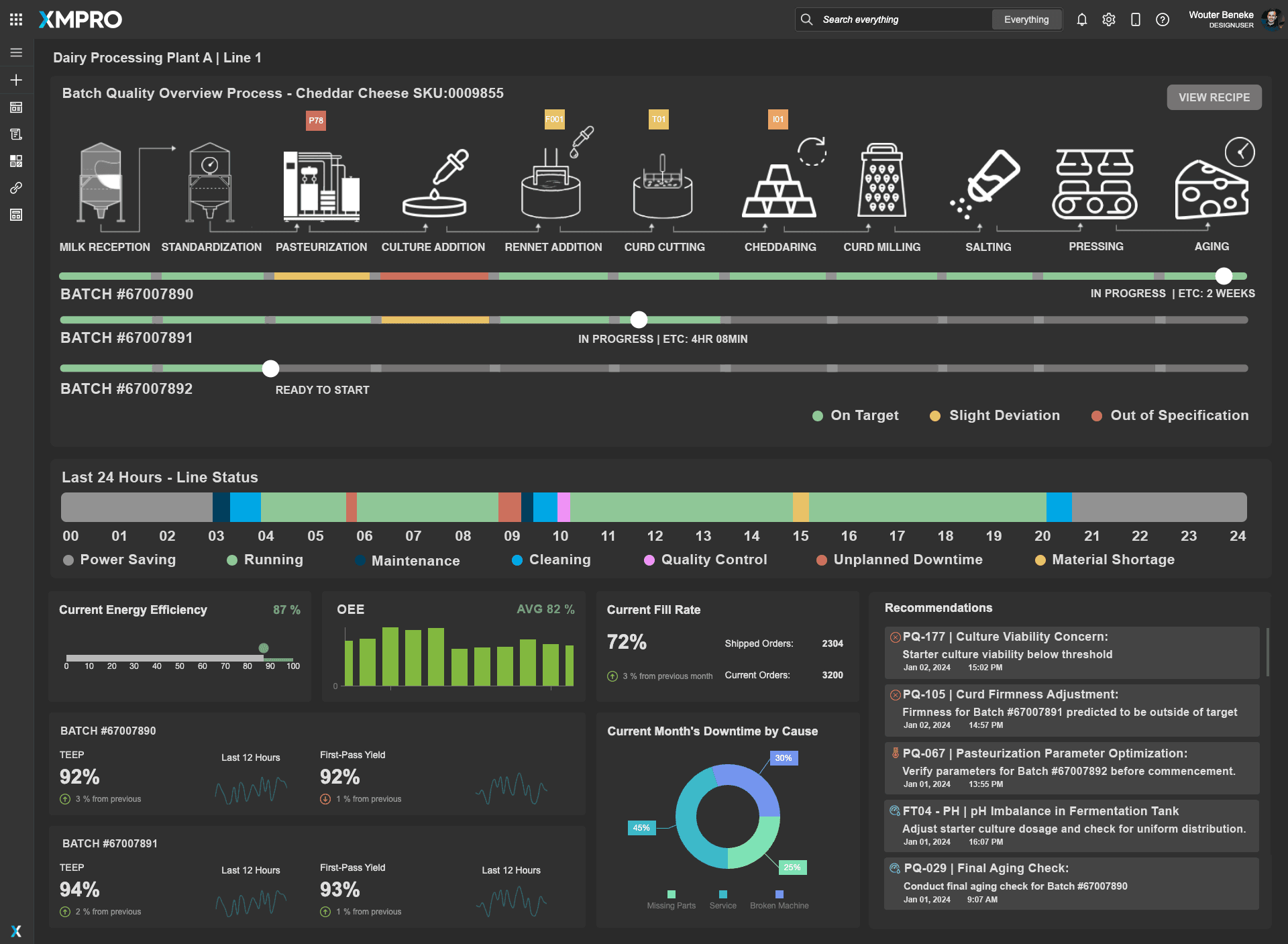
Figure1. Real-time Dairy Processing Plant Operations Dashboard
Comprehensive Dashboard for Dairy Plant Operations
This comprehensive operations dashboard is tailored for dairy plant managers and operators to oversee the cheese production process. It provides a complete view of the workflow from milk reception to cheese aging, displaying the current status of different batches and processing stages like standardization, pasteurization, and culture addition.
Batch Progress and Line Status:
The dashboard displays the progress of various cheese batches through their production stages, with detailed information on each batch’s status. Additionally, the ‘Last 24 Hours – Line Status’ section gives a color-coded timeline showing periods of running, maintenance, cleaning, quality control, and downtime.
Operational Efficiency Metrics:
Key performance indicators such as Overall Equipment Effectiveness (OEE) and energy efficiency are presented, alongside real-time updates on the fill rate of cheese production. The dashboard illustrates the plant’s operational efficiency, providing insights for potential improvements.
Predictive Recommendations:
XMPro’s system issues targeted recommendations to improve the cheese-making process, including alerts on culture viability concerns and adjustments for firmness and pasteurization parameters. It also suggests checks for pH balance in the fermentation tank and final aging checks, ensuring quality and consistency.
Granular Insights and Predictive Maintenance:
Detailed insights are available for each batch, with predictive analytics on equipment health and process efficiency. This includes monitoring Total Effective Equipment Performance (TEEP) and providing a breakdown of the current month’s downtime causes, helping to strategically plan maintenance and reduce potential interruptions.
Summary and Trend Analysis:
The dashboard offers a summary view of recent batch performance with trends in first-pass yield and a comprehensive look at operational data over time. It allows for quick assessments and informed decision-making to enhance production quality and efficiency.
User-Centric Interface:
With its user-friendly interface, the dashboard ensures that all information—from batch progress to efficiency metrics—is easily accessible, enabling efficient navigation and rapid retrieval of detailed data for strategic management.
This Dairy Processing Plant Operations Dashboard is an essential tool for monitoring and optimizing the cheese production line, enabling a proactive approach to quality control, maintenance, and operational excellence.”
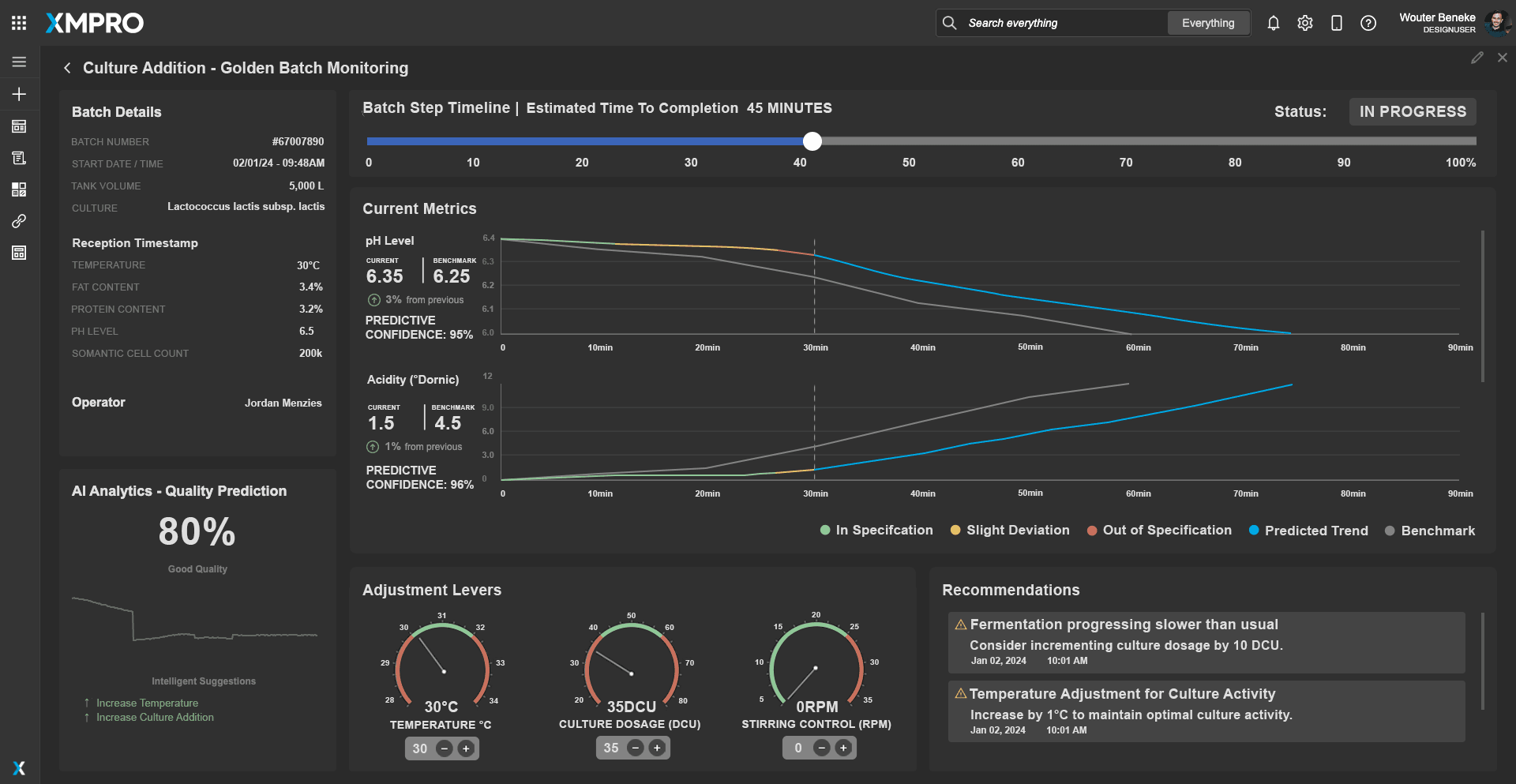
Figure 2. In-Depth Culture Addition Monitoring Dashboard for Dairy Processing
This dashboard offers a specialized view into the culture addition phase of dairy processing, an essential step in cheese and yogurt production. It provides dairy professionals with real-time data and analytics, ensuring precision and quality in the addition of cultures to milk batches.
Detailed Batch Analysis:
The XMPro Golden Batch Monitoring Dashboard presents comprehensive details of each culture addition batch, including the batch number, start date/time, and tank volume. It further provides the exact culture being used, in this case, Lactococcus lactis subsp. lactis, and tracks the reception timestamp along with critical parameters like temperature, fat content, protein content, pH level, and somatic cell count.
Process Timeline and Current Metrics:
A dynamic Batch Step Timeline is showcased, indicating the current stage and estimated time to completion for the culture addition process. Concurrently, the dashboard displays real-time metrics such as pH level and acidity, juxtaposed against benchmark values for immediate assessment of the process’s adherence to quality standards.
AI-Driven Quality Assessment:
The AI Analytics module offers a predictive quality rating, which in this example is 80% for good quality, accompanied by intelligent suggestions to optimize the process, such as increasing temperature or culture addition.
Adjustment Levers and Predictive Recommendations:
Operators are equipped with adjustment levers for fine-tuning the process parameters like temperature and culture dosage. The system also proactively generates recommendations based on real-time data; for example, it suggests incrementing culture dosage by 10 DCU to address fermentation pace or adjusting temperature to maintain optimal culture activity.
Operator Engagement:
The dashboard highlights the operator on duty, here identified as Jordan Menzies, linking process management directly to an individual for accountability and precision in operation handling.
Progress Indicators and Status Updates:
The progress bar at the top provides a quick glance at the batch status, clearly marked as ‘In Progress’, while a timeline graph beneath it offers insight into the specification adherence of the ongoing process.
The Culture Addition Monitoring Dashboard serves as a critical tool for dairy processors, enabling meticulous management of the culture addition stage to ensure product consistency, quality, and the successful production of dairy products.
Why XMPro iDTS for Dairy Processing Plant Operations?
XMPro’s Intelligent Digital Twin Suite (iDTS) delivers a suite of solutions specifically designed for the complex needs of managing dairy processing operations across multiple facilities. Here’s how XMPro iDTS revolutionizes dairy processing plant management:
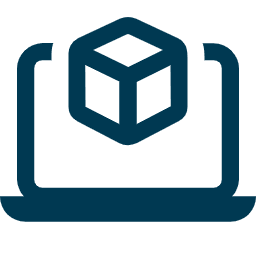
Advanced Intelligent Digital Twin Modeling:
XMPro iDTS constructs detailed digital twins of dairy processing plants, offering a virtual model that reflects the intricate operations of facilities spread across different regions. This capability facilitates in-depth analysis and simulation of processing equipment performance, including pasteurizers, separators, and fermentation tanks, under various operational conditions. It’s instrumental for optimizing processes in plants with diverse environmental and production demands.
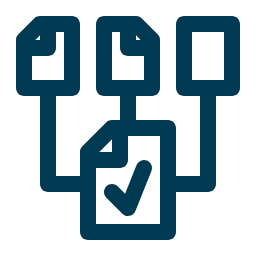
Advanced Sensor Data Integration & Transformation:
Integrating real-time data from sensors across all dairy processing equipment, XMPro iDTS captures critical metrics such as temperature, flow rates, and pressure levels. This extensive monitoring enables the identification and analysis of performance optimization opportunities throughout the dairy processing chain, ensuring uniform quality and efficiency.
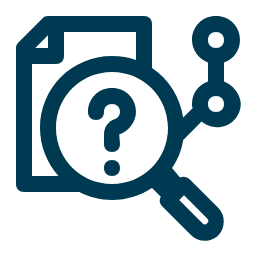
Predictive Analytics for Performance Enhancement:
Leveraging cutting-edge predictive analytics, XMPro iDTS anticipates potential issues and optimizes operational settings for each piece of equipment. This foresight allows for proactive adjustments in processes like pasteurization and fermentation, maximizing product quality and throughput while minimizing waste and downtime.
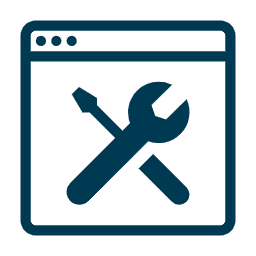
Maintenance Scheduling Optimization:
By analyzing equipment performance data, XMPro iDTS streamlines maintenance schedules, adopting a predictive maintenance model over a reactive one. This approach is crucial for coordinating maintenance activities across multiple facilities, enhancing equipment longevity and reducing operational interruptions.
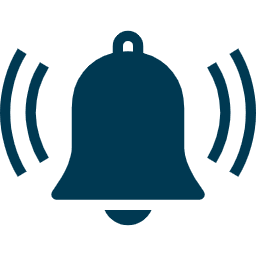
Real-Time Monitoring and Predictive Alerting:
Automated recommendations and alerts for equipment adjustments are generated based on real-time and predictive data analyses. This ensures that each piece of equipment, from homogenizers to cooling tanks, operates at optimal efficiency, significantly reducing the need for manual oversight.
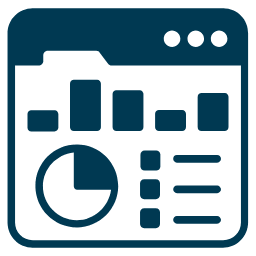
Customizable and Interactive Dashboards:
XMPro iDTS provides customizable dashboards that offer real-time insights into the health and performance of equipment across all dairy processing plants. These dashboards are designed to be interactive, enabling detailed scrutiny of specific operational aspects and supporting centralized management decisions.
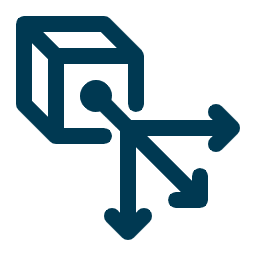
Scalability and Flexibility – Start Small, Scale Fast:
Designed to accommodate dairy operations of any scale, XMPro iDTS’s modular architecture allows for seamless integration and adaptability. This scalability ensures that dairy processing plants can efficiently manage operations as they expand or adapt to changing market demands.
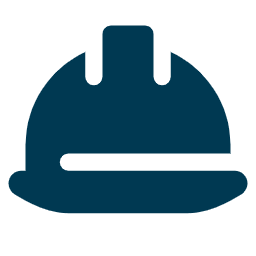
Enhanced Safety & Operational Efficiency:
XMPro iDTS boosts operational safety by identifying potential hazards and inefficiencies in the processing line, ensuring that all equipment operates within safe and optimal parameters. This contributes to a safer working environment and more efficient production processes.
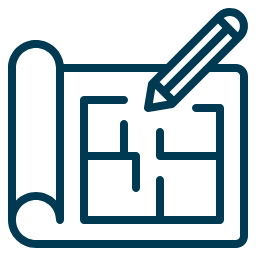
XMPro Blueprints – Quick Time to Value:
Offering quick time-to-value, XMPro Blueprints facilitate rapid deployment of digital twin solutions across dairy processing operations. These templates are built on industry best practices, ensuring that plants can quickly realize the benefits of digital transformation.
XMPro iDTS uniquely addresses the challenges of dairy processing plant operations by offering a holistic, predictive, and integrated management solution. Its advanced digital twin technology, combined with comprehensive data analytics and customizable dashboards, empowers dairy processors to achieve unparalleled operational efficiency, product quality, and safety across multiple facilities.
