Condition Monitoring & Predictive Maintenance Solution for Mainline Conveyors in the Mining Industry
Introduction
In large-scale mining operations, conveyor belts are critical for transporting materials efficiently. Long conveyors, in particular, face significant challenges due to their extended length and continuous operation. Ensuring their optimal performance and preventing unexpected failures is essential for maintaining productivity and minimizing downtime. XMPro’s Long Conveyor Condition Monitoring & Predictive Maintenance Solution offers comprehensive monitoring and predictive maintenance capabilities to address these challenges.
Typical Problems Faced:
- Wear and Tear: Continuous operation and abrasive materials lead to rapid wear and tear, necessitating regular maintenance.
- Downtime and Failures: Unexpected breakdowns can cause significant operational disruptions and financial losses.
- Efficiency Optimization: Maintaining optimal performance while managing energy consumption and load distribution.
- Safety Risks: Conveyor failures can pose safety hazards to personnel and equipment.
- Data Overload: Handling and analyzing vast amounts of operational data to derive actionable insights.
The Solution: XMPro iBOS for Long Conveyor Condition Monitoring & Predictive Maintenance Solution
XMPro’s Long Conveyor Condition Monitoring & Predictive Maintenance Solution leverages real-time data integration, advanced analytics, and predictive maintenance to enhance the reliability and efficiency of conveyor systems.
By adopting a data-centric approach, it substantially increases the accuracy, efficiency, and scalability of conveyor management, which is crucial for maintaining stringent operational and safety standards.
Key Features:
Real-Time Monitoring and Control: XMPro’s solution provides a centralized platform for real-time monitoring and control of conveyor systems, offering insights into operational parameters such as speed, load, and vibration.
Predictive Analytics for Maintenance Optimization: The system employs advanced predictive analytics to forecast potential failures and maintenance needs. By leveraging machine learning models, it can predict when components are likely to fail and recommend timely interventions.
Digital Twin Technology: XMPro’s Intelligent Digital Twin Suite (iDTS) creates detailed digital replicas of conveyor systems. These digital twins simulate real-world conditions and enable scenario planning, optimizing maintenance schedules and operational strategies without disrupting actual operations.
Automated Maintenance Scheduling: The platform automates maintenance scheduling based on real-time data and predictive analytics, ensuring that maintenance activities are conducted just in time. This approach reduces downtime and operational costs by preventing unnecessary maintenance interventions and addressing issues before they escalate.
Integration with IoT and Data Sources: XMPro integrates data from various IoT devices and operational systems, providing a comprehensive view of equipment health and performance. This integration facilitates the continuous collection and analysis of data, enhancing the accuracy of predictive models.
Customizable Dashboards and Reporting: XMPro offers customizable dashboards that provide actionable insights and detailed reports on conveyor system performance. These dashboards help in tracking key performance indicators (KPIs), compliance, and operational efficiency.
Enhanced Safety and Risk Management: The solution includes features for operational safety intelligence, highlighting potential hazards and recommending control measures. It helps in mitigating risks associated with equipment failures and ensuring a safer working environment.
Scalability and Flexibility: Designed to scale with the needs of the mining industry, XMPro’s solution supports the expansion of operations while maintaining the flexibility required to adapt to new challenges and opportunities.
By implementing XMPro’s Long Conveyor Condition Monitoring & Predictive Maintenance Solution, mining operations can achieve significant improvements in efficiency, reliability, and cost savings. The use of predictive maintenance principles ensures that maintenance is conducted based on actual equipment conditions, leading to reduced downtime, extended equipment lifespan, and enhanced overall operational performance
How XMPro iBOS Modules Work Together To Create This Condition Monitoring Solution
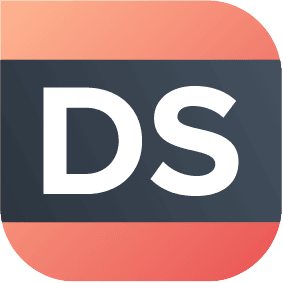
XMPro Data Stream Designer
XMPRO’s Data Stream Designer lets you visually design the data flow and orchestration for your real-time applications. Our drag & drop connectors make it easy to bring in real-time data from a variety of sources, add contextual data from systems like EAM, apply native and third-party analytics and initiate actions based on events in your data.
Figure 2: Conveyor Health Condition Monitoring Data Stream
This conveyor condition monitoring data stream ingests telemetry data from all conveyors, cleans it, and broadcasts it to various endpoints. The data is contextualized with information about the conveyor make, model, and operational context. It then undergoes several transformations and functions: the data is cleaned up for recommendations, rounded for precision, and filtered to exclude irrelevant belts. The processed data is used to view asset data and evaluate failure recommendation rules. This comprehensive data flow ensures precise, efficient, and actionable insights into the health of the conveyor system, enabling proactive maintenance and enhanced operational reliability.
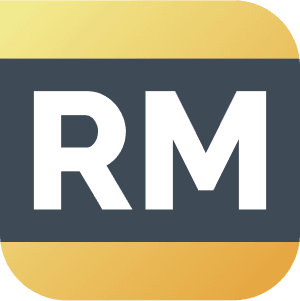
Recommendation Manager
XMPRO Recommendations are advanced event alerts that combine alerts, actions, and monitoring. You can create recommendations based on business rules and AI logic to recommend the best next actions to take when a certain event happens. You can also monitor the actions against the outcomes they create to continuously improve your decision-making.
Figure 1. Amperage Exceeded Threshold Recommendation
This recommendation identifies an issue with the amperage exceeding the defined threshold, indicating a differential greater than 30%. The event data includes details such as drive amps, reading number, timestamp, health score, conveyor speed, and asset number. Users can add notes, mark the recommendation as solved or a false positive, assign the recommendation, share it, and create a work request with special instructions if necessary. This structured approach ensures that potential issues are efficiently addressed and resolved to maintain optimal conveyor performance.
Figure 2. Configure with Granular Rule Logic
This amperage threshold recommendation configuration allows users to set up granular rule logic for monitoring conveyor conditions. The interface enables selecting metrics such as drive amps and setting specific thresholds to trigger alerts. Users can categorize recommendations, enable execution order, and auto-escalate critical issues. The configuration includes setting impact metrics, defining rule logic with conditions (e.g., drive amps greater than 50 but less than 70), and linking to forms for work requests. This detailed setup ensures precise monitoring and timely intervention for maintaining conveyor system efficiency.
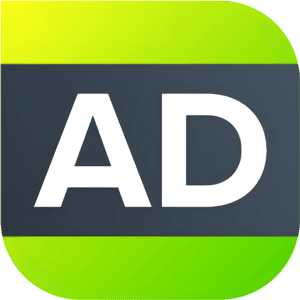
XMPro App Designer
The XMPro App Designer is a no code event intelligence application development platform. It enables Subject Matter Experts (SMEs) to create and deploy real-time intelligent digital twins without programming. This means that SMEs can build apps in days or weeks without further overloading IT, enabling your organization to accelerate and scale your digital transformation.
Figure 1: Real-Time Mine Conveyor Overview
The Real-Time Mine Conveyor Overview dashboard provides a comprehensive visualization of the entire conveyor system, enabling operators to monitor and manage conveyor operations effectively.
Key Dashboard Features:
Conveyor Layout Visualization:
- A detailed map of the conveyor system, displaying the real-time status of each segment and highlighting areas with issues.
Predictive Maintenance Alerts:
- Predictive alerts for potential failures, generated by advanced machine learning models analyzing sensor data. This feature allows maintenance teams to address issues before they lead to equipment failure.
Current Open Recommendations:
- A list of current maintenance recommendations based on predictive analytics, categorized by severity (high, medium, low). This helps prioritize maintenance activities and allocate resources efficiently.
Recommendations and Resolution Metrics:
- Metrics on the number of recommendations generated, assigned, and resolved over the last seven days. This provides insights into the effectiveness of the maintenance strategy and helps identify areas for improvement.
Resolution Time Analysis:
- Detailed analysis of the time taken to resolve maintenance issues, from generation to assignment and resolution. This helps in optimizing maintenance workflows and improving response times.
Benefits for the Client:
- By providing real-time insights and predictive maintenance alerts, this dashboard helps in minimizing unplanned downtime, reducing maintenance costs, and enhancing the overall efficiency of the conveyor system. The ability to visualize and manage the entire conveyor system from a single platform enables quicker decision-making and more effective resource allocation.
This comprehensive overview enables operators and maintenance teams to monitor conveyor performance effectively, identify potential issues early, and take corrective actions to maintain high operational standards and equipment reliability.
Figure 2: Mainline Conveyor #16
The Mainline Conveyor #16 dashboard offers an in-depth analysis of the primary and secondary motors, providing real-time data and predictive maintenance insights to ensure optimal performance and prevent unexpected failures.
Key Dashboard Features: Conveyor Details:
- Section, Belt Number, and ID: Displays the specific section, belt number, and identification for Mainline Conveyor #16, allowing for easy reference and management.
- Motor Make: Information on the make of the motors used in the conveyor system.
Primary and Secondary Motor Differentials:
- Differential Gauges: Show the differential between the primary and secondary motors’ performance, including current draw and load distribution.
- Benefit: Helps in identifying imbalances and inefficiencies, ensuring that the motors are operating in harmony and preventing potential overloads.
Motor Performance Metrics:
- Real-Time Data: Displays real-time data on motor amps, temperature, and vibration for each motor (Motor #1 to Motor #4).
- Benefit: Continuous monitoring of these parameters helps in detecting anomalies early and ensuring the motors operate within safe and optimal ranges.
Predictive Maintenance Alerts:
- Automated Alerts: Predictive alerts generated based on real-time data and predictive analytics, indicating issues such as high motor current, low efficiency, and mechanical faults.
- Benefit: Enables proactive maintenance by alerting operators to potential issues before they lead to significant failures, thus reducing downtime and maintenance costs.
Recommendations:
- Maintenance Actions: Provides specific recommendations for maintenance actions, such as adjusting couplings or monitoring motor currents.
- Benefit: Ensures timely and appropriate maintenance interventions, enhancing the reliability and efficiency of the conveyor system.
Work Request History:
- Maintenance Log: Detailed log of past maintenance activities, including work request numbers, descriptions, statuses, and dates.
- Benefit: Provides a comprehensive history of maintenance activities, supporting continuous improvement and informed decision-making.
Value for the Client:
- Enhanced Operational Efficiency: By providing detailed real-time data and predictive maintenance insights, this dashboard helps operators maintain optimal motor performance and prevent unexpected failures.
- Proactive Maintenance Management: Automated alerts and maintenance recommendations ensure that issues are addressed promptly, reducing the risk of costly downtime.
- Comprehensive Maintenance Tracking: The detailed work request history aids in tracking past issues and repairs, facilitating continuous improvement and better resource allocation.
- Improved Decision-Making: The combination of real-time data, predictive analytics, and actionable recommendations supports informed decision-making, enhancing overall operational performance and reliability.
This detailed analysis and predictive maintenance approach ensure that Mainline Conveyor #16 operates efficiently and reliably, minimizing downtime and maintenance costs while maximizing productivity.
Figure 3: Conveyor Belt #22637
The Conveyor Belt #22637 dashboard provides a comprehensive overview of the operational status and performance metrics for Conveyor Belt #22637, offering real-time data and predictive maintenance insights to optimize performance and prevent unexpected failures.
Key Dashboard Features: Differentials:
- Motor Differentials: Tracks the differentials between the motors (Motor 1, Motor 2, Motor 3, Motor 4) over time.
- Benefit: Identifies imbalances and inefficiencies, allowing operators to address issues that could lead to motor strain or failure.
Tonnage:
- Material Flow Monitoring: Displays the tonnage transported by the conveyor over specific periods.
- Benefit: Helps ensure consistent material flow and identify any discrepancies in load distribution that could impact conveyor performance.
Amperage:
- Current Draw: Shows the current draw of each motor, helping to monitor electrical consumption and detect anomalies.
- Benefit: Provides insights into the energy efficiency of the conveyor system and identifies potential electrical issues before they escalate.
Primary and Secondary Draw:
- Total Amps Monitoring: Displays the total amperage drawn by the primary and secondary drums.
- Benefit: Helps in managing the load on the conveyor system, ensuring that it operates within safe and optimal parameters.
Real-time Alerts and Recommendations:
- Alert Indicators: Highlights areas where issues such as exceeding motor thresholds or operational anomalies have been detected.
- Recommendations: Provides actionable recommendations for addressing each alert, such as maintenance actions or operational adjustments.
- Benefit: Ensures timely interventions to address potential problems, reducing downtime and preventing equipment damage.
Current Open Recommendations:
- Categorized Alerts: Lists current maintenance recommendations based on predictive analytics, categorized by severity (high, medium, low).
- Benefit: Helps prioritize maintenance activities and ensures that critical issues are addressed promptly.
Work Request History:
- Maintenance Log: Detailed log of past maintenance activities, including work request numbers, descriptions, statuses, and dates.
- Benefit: Provides a comprehensive history of maintenance activities, supporting continuous improvement and informed decision-making.
Value for the Client:
- Enhanced Operational Visibility: The dashboard offers a clear and immediate understanding of the conveyor system’s health and performance, enabling operators to quickly identify and address issues.
- Proactive Maintenance Management: Real-time alerts and predictive maintenance recommendations enable proactive maintenance, reducing the risk of unexpected failures and minimizing downtime.
- Efficient Resource Allocation: Categorizing alerts by severity and tracking maintenance history helps prioritize maintenance efforts and allocate resources effectively.
- Improved Decision-Making: The comprehensive overview and detailed insights support informed decision-making, enhancing overall operational efficiency and reliability.
By leveraging the real-time data and predictive maintenance capabilities of the XMPro Conveyor Belt #22637 dashboard, mining operations can achieve significant improvements in efficiency, reliability, and cost savings. This comprehensive approach ensures that maintenance is conducted based on actual equipment conditions, leading to reduced downtime, extended equipment lifespan, and enhanced overall operational performance.
Figure 4: Real-Time Mine Health Overview The Real-Time Mine Health Overview dashboard provides a holistic view of the mine’s operational health, highlighting key metrics, alerts, and the status of various components. This dashboard is essential for maintaining overall mine efficiency and safety.
Key Dashboard Features: Conveyors with Open Alerts:
- Alert Visualization: Displays the number of open alerts for each conveyor, categorized by severity (high, medium, low).
- Benefit: Allows operators to quickly identify conveyors with issues and prioritize maintenance based on alert severity.
Current Work Order Status:
- Work Order Distribution: Shows the status of current work orders, categorized as planning, waiting, or available.
- Benefit: Provides a clear picture of ongoing maintenance activities and helps in managing maintenance workflows efficiently.
Value Tracking:
- Criticality Index: Tracks the number of events based on criticality over different time frames (30, 60, 90 days).
- Benefit: Helps prioritize maintenance activities based on the criticality of the events, ensuring that the most pressing issues are addressed first.
Metrics for the Last 4 Weeks:
- Operational Metrics: Displays key performance indicators for the last four weeks, including the number of new alerts, work requests not actioned, completed work orders, false positives, and total alerts closed.
- Benefit: Provides insights into the mine’s operational performance over time and helps identify trends and areas for improvement.
Borers Health Overview:
- Health Scores and Alerts: Shows the health scores of different borers, along with the number of alerts over the last four weeks.
- Benefit: Allows for targeted maintenance on borers that are showing signs of deterioration, preventing failures and maintaining operational efficiency.
Resolution Time Analysis:
- Resolution Metrics: Tracks the time taken to resolve maintenance issues, from generation to assignment and resolution.
- Benefit: Ensures timely resolution of maintenance issues, optimizing workflow efficiency and improving response times.
Value for the Client:
- Enhanced Operational Visibility: The comprehensive overview of the mine’s health allows operators to monitor critical systems and components effectively, ensuring that all parts of the mine are operating efficiently.
- Proactive Maintenance Management: Real-time alerts and actionable recommendations enable proactive maintenance, reducing the risk of unexpected failures and minimizing downtime.
- Efficient Resource Allocation: By categorizing alerts and tracking resolution times, the dashboard helps prioritize maintenance activities and allocate resources more effectively.
- Improved Decision-Making: The detailed insights and metrics support informed decision-making, enhancing overall operational performance and reliability.
By utilizing the Real-Time Mine Health Overview dashboard, mining operations can achieve significant improvements in efficiency, reliability, and safety. The combination of real-time data, predictive maintenance insights, and comprehensive visualization ensures that all aspects of the mine’s operations are closely monitored and optimized.
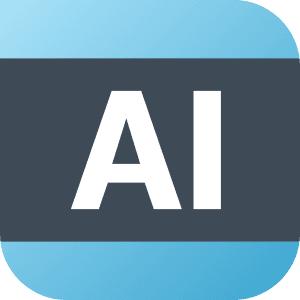
XMPro AI (Optional)
Experience the transformative power of XMPro’s Intelligent Business Operations Suite (iBOS) – Featuring comprehensive AI capabilities, XMPro iBOS helps to significantly increase product yield, drastically reduce downtime, and ultimately eliminate unexpected business events.
CLIENT CASE STUDY
CLIENT CHALLENGE:
In order to maximize underground mining operations, the underground conveyor system, a frequent cause of unplanned downtime, needed to reduce its downtime by 30% as an initial target for a predictive maintenance solution
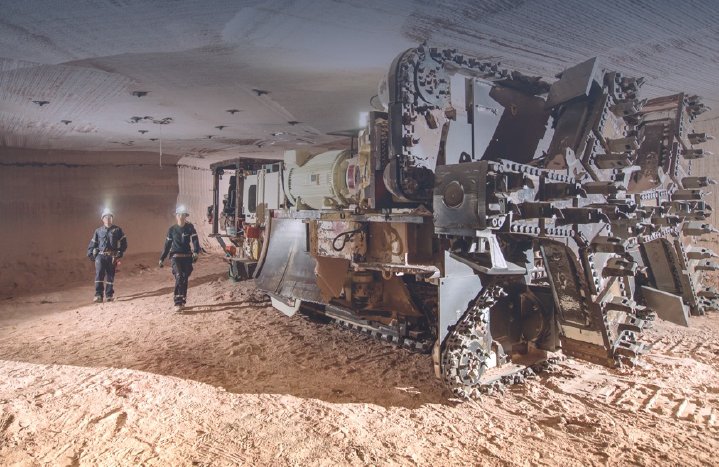
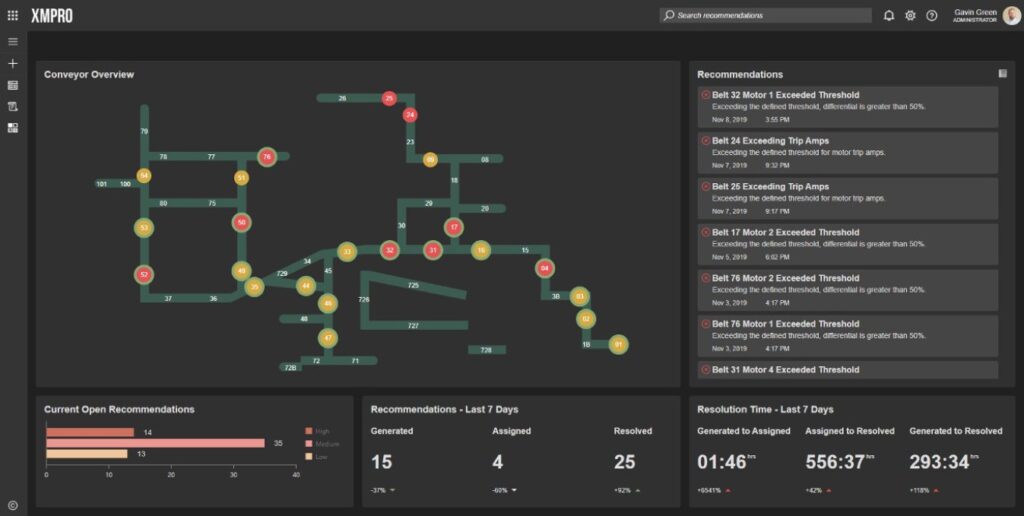
XMPRO SOLUTION
XMPro actively monitors 52 conveyors (spanning over 80+km) in real time, predicting fluid coupling and lagging failures with prescriptive recommendations.
BENEFITS:
Within five months, the solution identified a potential saving of 184 hours of borer downtime, equating to 44k product tonnes. Exceeding the target, the solution achieved over a 80% reduction in downtime for fluid coupling failures. It now monitors multiple asset types across several mines
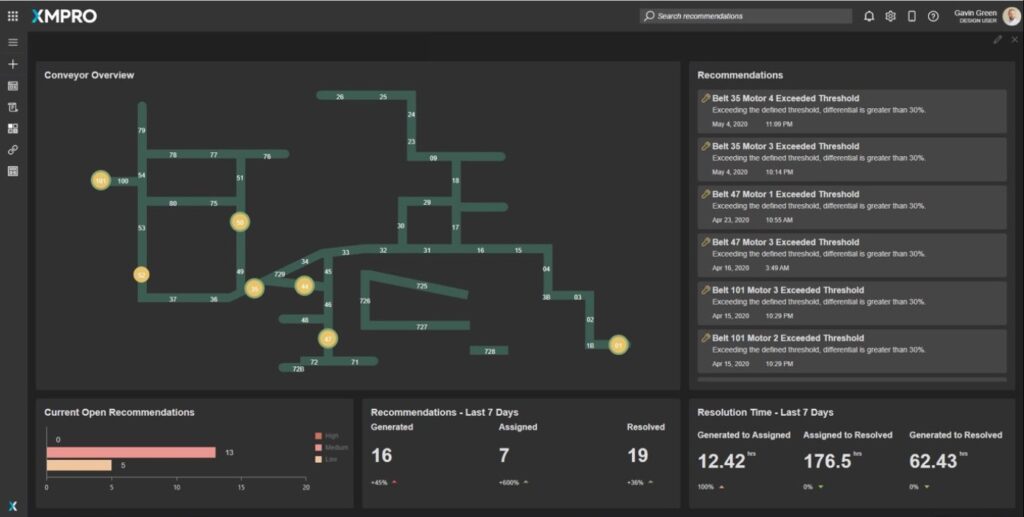
Use XMPro Blueprints for Quick Time To Value
Easily import Blueprints, Accelerators and Patterns into your environment, providing a starting point for configuring your own solutions.
Why XMPro iBOS for Long Conveyor Condition Monitoring & Predictive Maintenance in the Mining Industry?
XMPro’s Intelligent Business Operations Suite (iBOS) is specifically engineered to address the complexities of monitoring and maintaining long conveyor systems in mining operations. Here are the key reasons why XMPro iBOS stands out as the ideal solution:
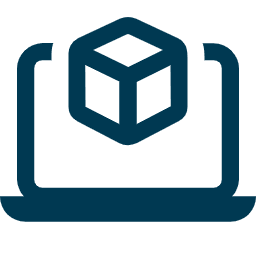
Advanced Intelligent Digital Twin Modeling:
XMPro iBOS creates sophisticated digital twins for each conveyor system, providing a virtual representation that mirrors the real-world conditions of the conveyors. This feature enables detailed analysis and simulation of conveyor performance under various operational scenarios, crucial for managing extensive conveyor networks in mining operations.
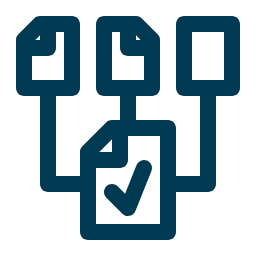
Advanced Sensor Data Integration & Transformation:
The suite integrates real-time data from a variety of sensors on conveyors, including speed, load, vibration, and temperature. This comprehensive monitoring allows for the identification of optimization areas across the conveyor system, ensuring consistent performance and efficiency.
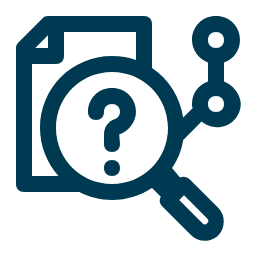
Predictive Analytics for Performance Enhancement:
Utilizing advanced predictive analytics, XMPro iBOS forecasts potential performance issues and identifies optimal operational settings for each conveyor segment, considering the unique operational conditions. This predictive approach enables proactive adjustments, maximizing efficiency and minimizing downtime.
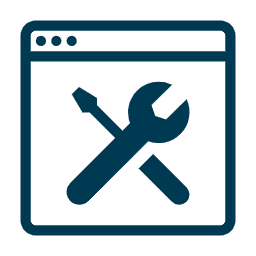
Maintenance Scheduling Optimization:
XMPro iBOS analyzes performance data to optimize maintenance schedules, transitioning from a reactive to a predictive maintenance approach. This strategy reduces downtime and extends the lifespan of conveyor components, which is particularly beneficial for managing maintenance resources efficiently.
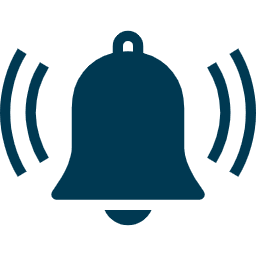
Real-Time Monitoring and Predictive Alerting:
The platform generates automated recommendations for adjusting conveyor settings based on real-time data and predictive insights. This feature ensures that conveyors operate at peak efficiency, with minimal manual intervention.
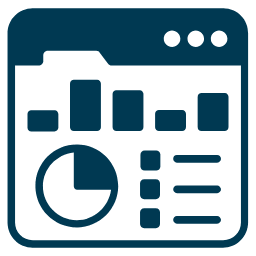
Configurable and Interactive Dashboards:
XMPro iBOS features configurable dashboards that provide real-time insights into the performance of conveyor systems. These dashboards are interactive, allowing operators to drill down into specific aspects of conveyor operation, facilitating centralized control and decision-making.
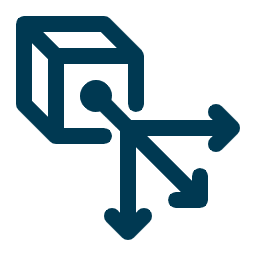
Scalability and Flexibility – Start Small, Scale Fast:
XMPro iBOS offers scalable and flexible solutions, ideal for conveyor systems of varying sizes and complexities. Its modular design ensures easy integration and adaptability, allowing for quick deployment and scalability as the conveyor network expands.
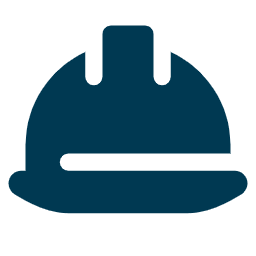
Enhanced Safety & Operational Efficiency:
The suite enhances operational safety by predicting and mitigating potential risks associated with conveyor operation. It improves overall operational efficiency by ensuring conveyors operate within optimal parameters.
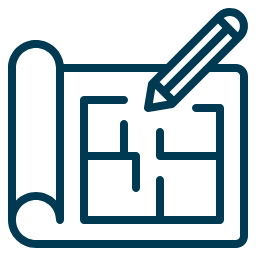
XMPro Blueprints – Quick Time to Value:
XMPro Blueprints provide a rapid path to value realization for mining operations. These pre-configured templates are designed for quick implementation, incorporating best practices and industry standards.
By implementing XMPro iBOS for Long Conveyor Condition Monitoring & Predictive Maintenance, mining operations can achieve significant improvements in efficiency, reliability, and safety. The combination of advanced predictive maintenance capabilities, comprehensive digital twin technology, and real-time data integration makes XMPro iBOS the ideal solution for optimizing conveyor system performance and enhancing overall operational effectiveness.
